Refractory gunning machine for blast furnace kiln
Refractory Gunning Machine for Blast Furnace Kiln is a key equipment used in the modern steel industry to repair and maintain the lining of blast furnaces. It uses high-pressure spraying technology to quickly and evenly cover the refractory mixture on the damaged refractory surface to form a new protective layer.
The refractory gunning machine for blast furnace kilns is a special repair equipment for the wear and erosion of refractory materials in the blast furnace lining. It uses high-pressure spraying technology to quickly and evenly cover the damaged surface with refractory materials to form a new protective layer.
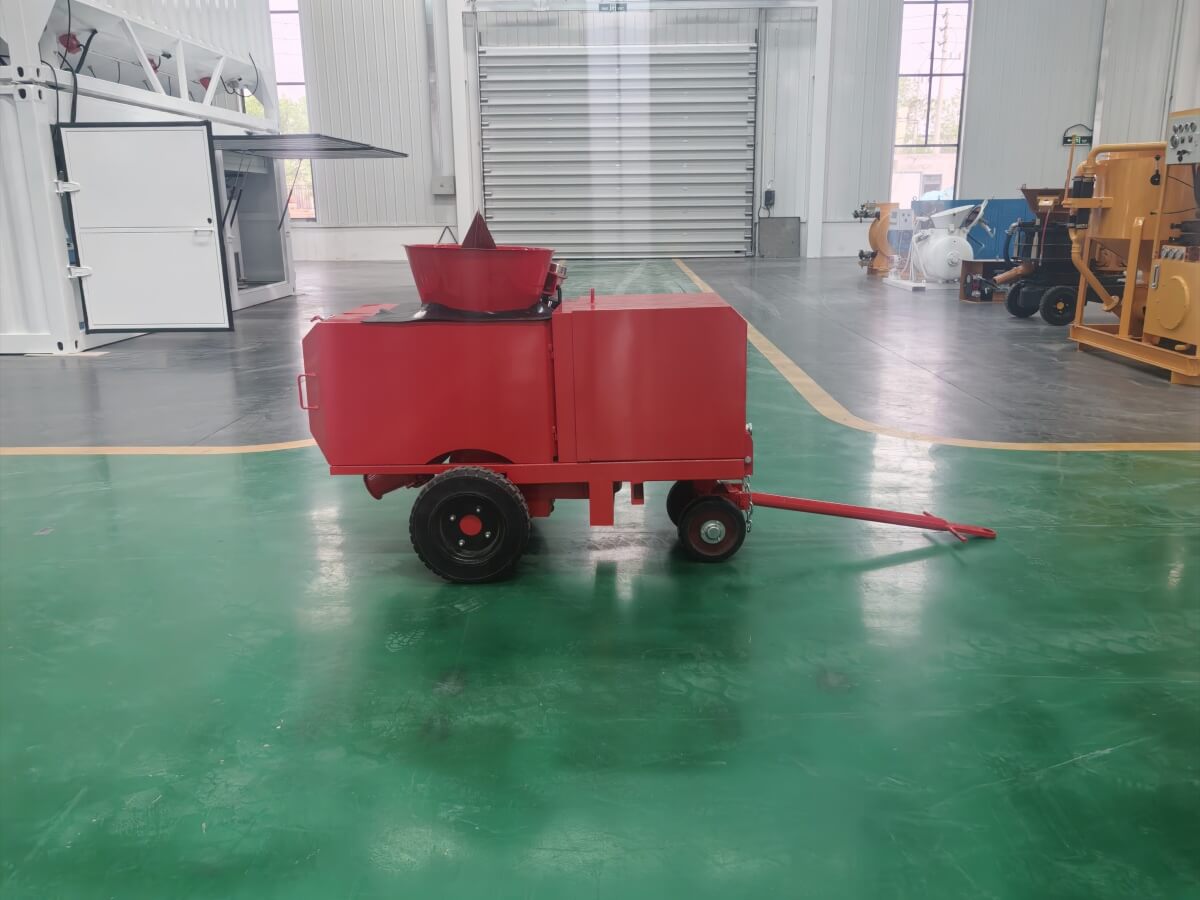
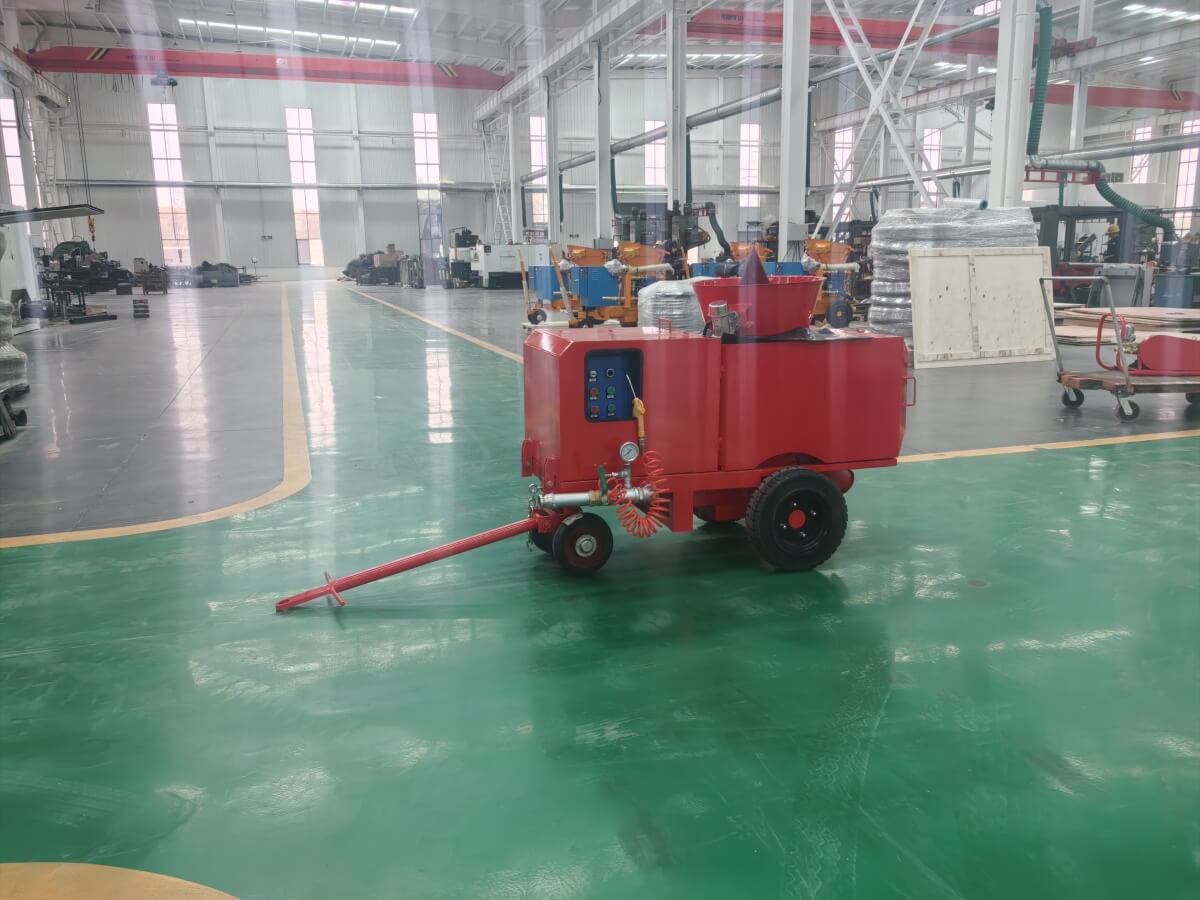
Core features of the refractory gunning equipment:
High-pressure spraying system
Use high-pressure airflow (usually pressure ≥5kg/cm²) to spray refractory materials at high speed onto the surface of the blast furnace lining to ensure that the material is tightly combined with the matrix.
Gunning capacity: 40-120kg/min, adapted to different repair thickness requirements.
Material conveying and mixing system
Equipped with a screw conveyor or pneumatic conveying device to achieve continuous and stable supply of refractory materials.
Dry and semi-dry mixing technology to ensure material uniformity and reduce rebound loss.
Automation control system
PLC intelligent control, real-time adjustment of spraying pressure, speed and material ratio to improve repair accuracy.
Remote operation function to reduce the risk of manual operation in the blast furnace.
Safety and environmental protection design
The equipment is equipped with explosion-proof devices and dust recovery systems to ensure safe operation and reduce environmental pollution.
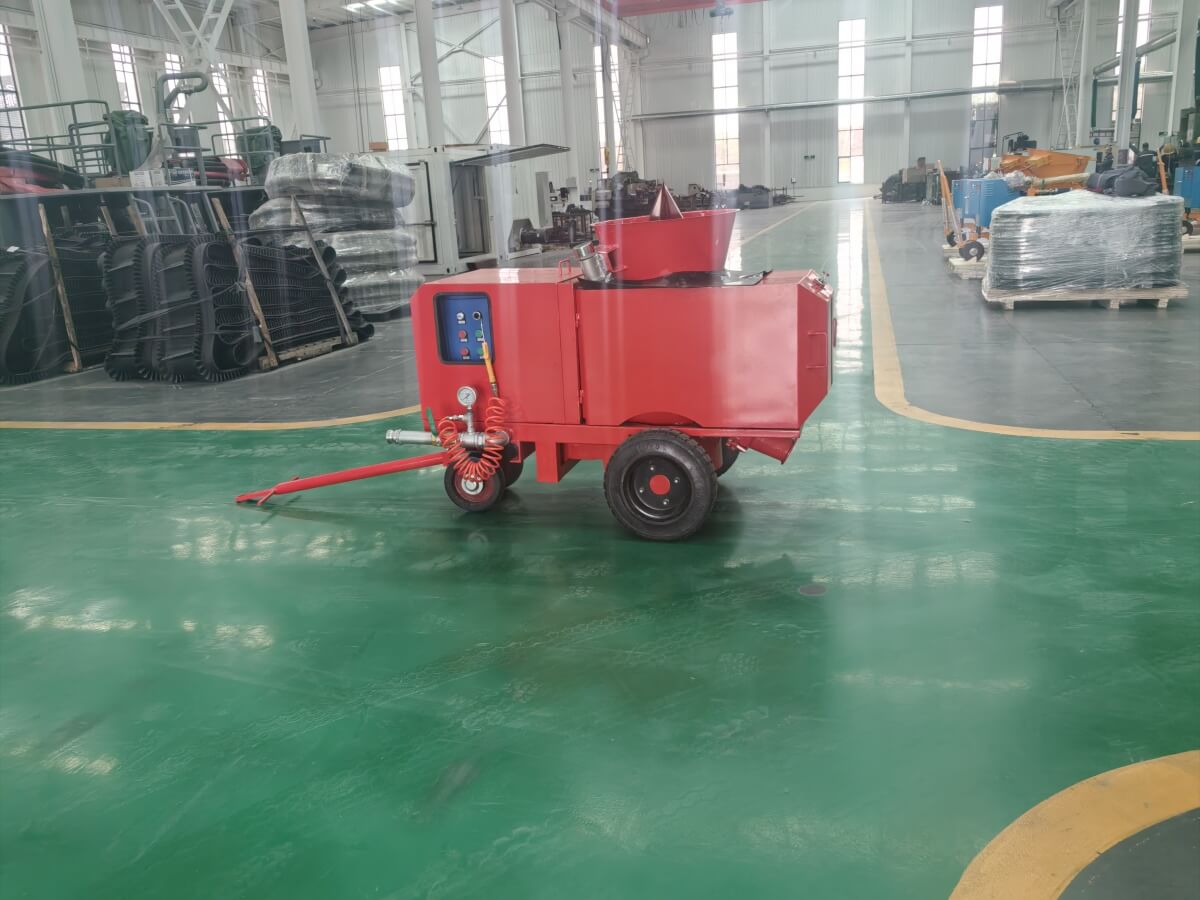
Application advantages of refractory gunning equipment:
Efficient repair
The spraying speed can reach 40-120kg/min, which significantly shortens the downtime of blast furnace maintenance and improves production efficiency.
Extend furnace life
Timely repair can effectively prevent further damage to the blast furnace lining and extend the service life of the blast furnace.
Reduce maintenance costs
Reduce manual repair work, reduce labor intensity and safety risks, and reduce refractory consumption.
Strong adaptability
Customized spraying can be performed for different parts of the blast furnace (such as furnace bottom, furnace wall, and tuyere area) to meet diverse repair needs.