Cement grout mixing plant for drilling project
The cement grout mixing plant for drilling project can be configured for continuous mixing to meet high-volume demands or batch mixing for smaller, specialized projects. High-speed forced-action mixers or planetary mixers are employed to achieve thorough hydration of cement particles, producing a lump-free, homogeneous slurry.
Cement grout mixing plant is used to make continuous cement slurry, widely used in drilling projects:
Well Sealing and Grouting:
In geothermal, water well, and oil/gas drilling, the plant produces cement grout for sealing annular spaces, preventing groundwater contamination, and stabilizing boreholes.
Foundation Stabilization:
For drilling projects involving deep foundations or soil improvement, the grout is used to reinforce weak soils and enhance load-bearing capacity.
Tunneling and Mining:
In underground construction, the plant supplies grout for rock bolting, shotcrete applications, and sealing water inflows in tunnels and mines.
Geotechnical Engineering:
The grout is used for soil nailing, slope stabilization, and ground anchor installation, ensuring the safety and durability of structures.
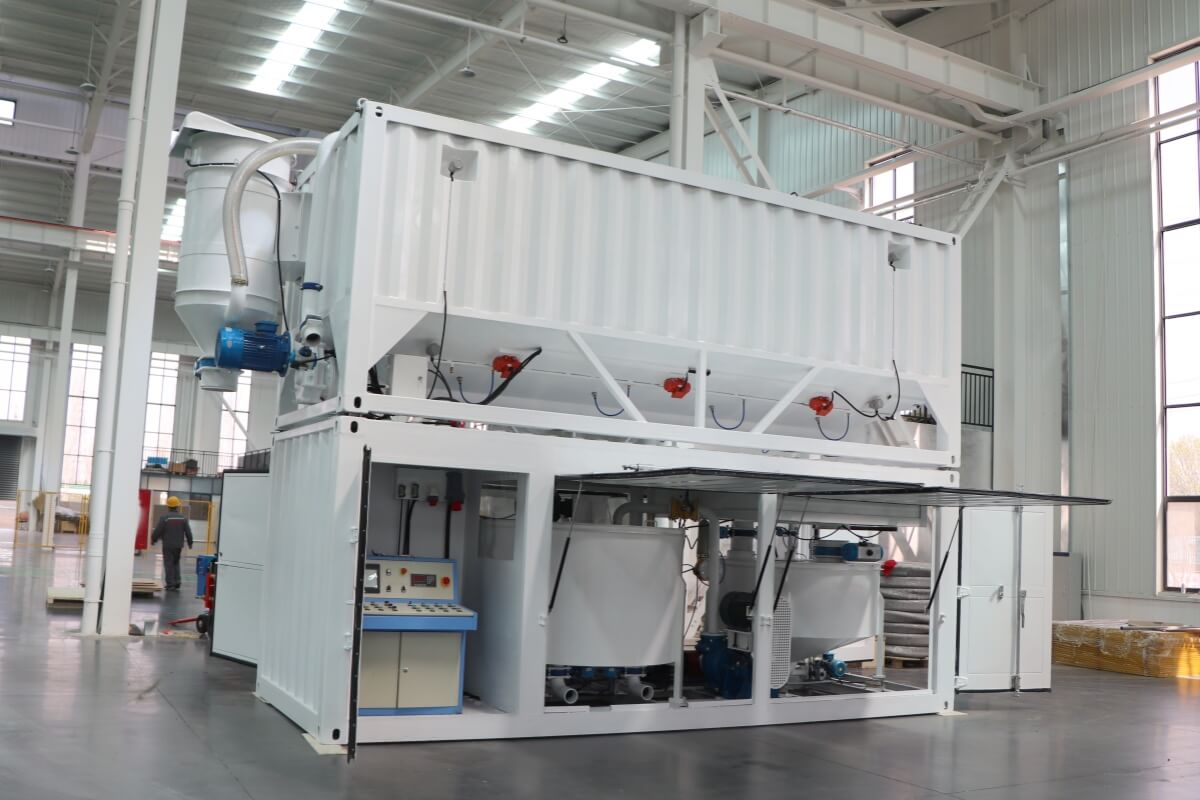
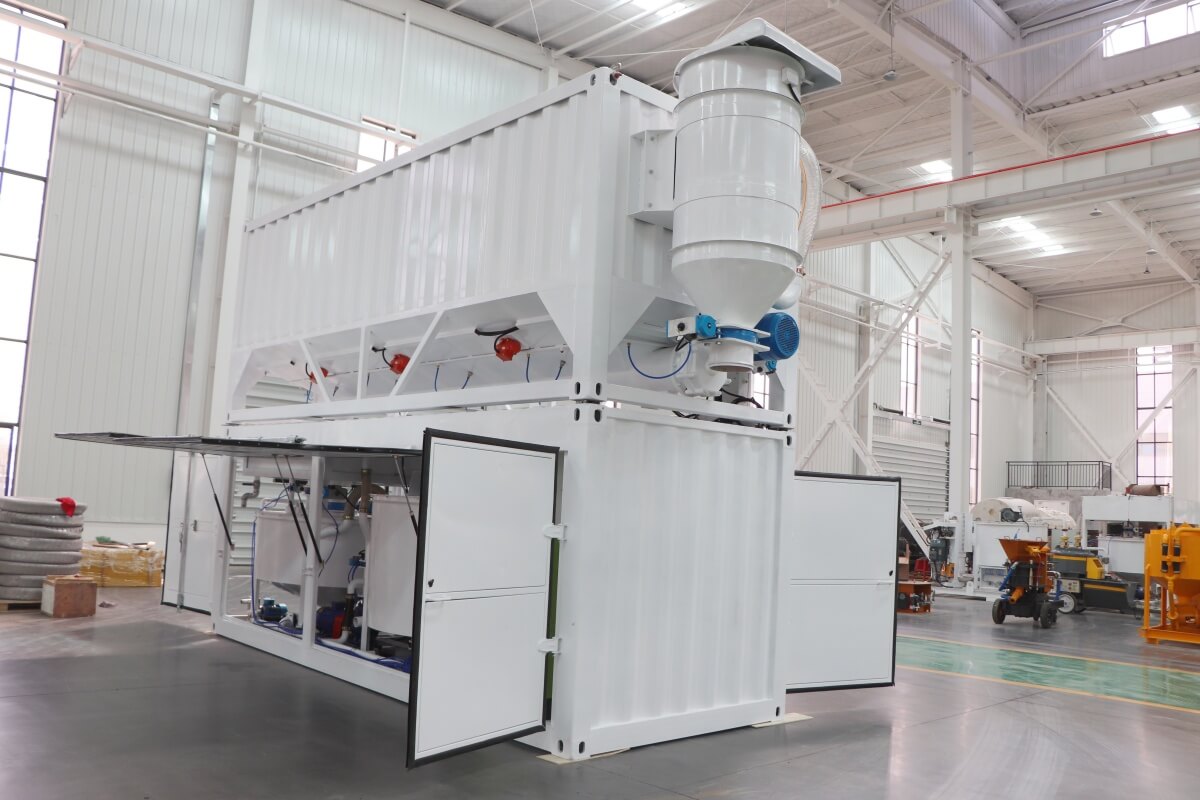
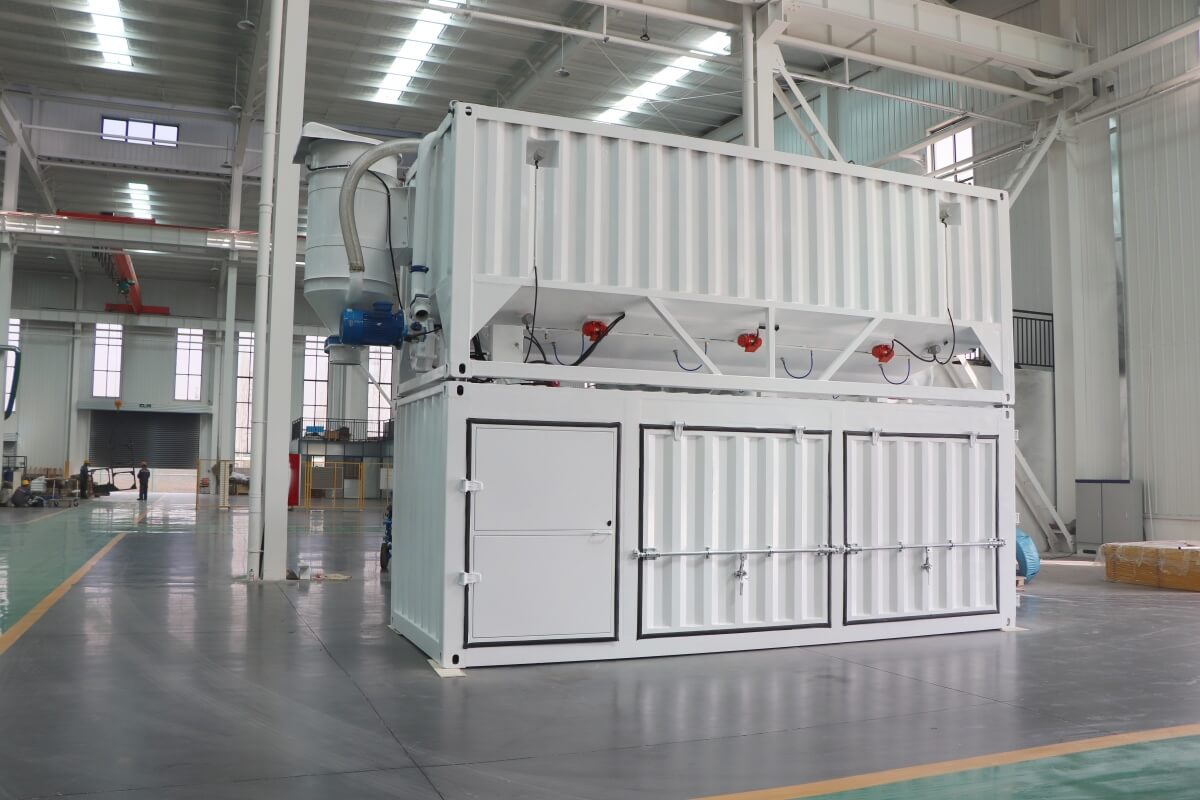
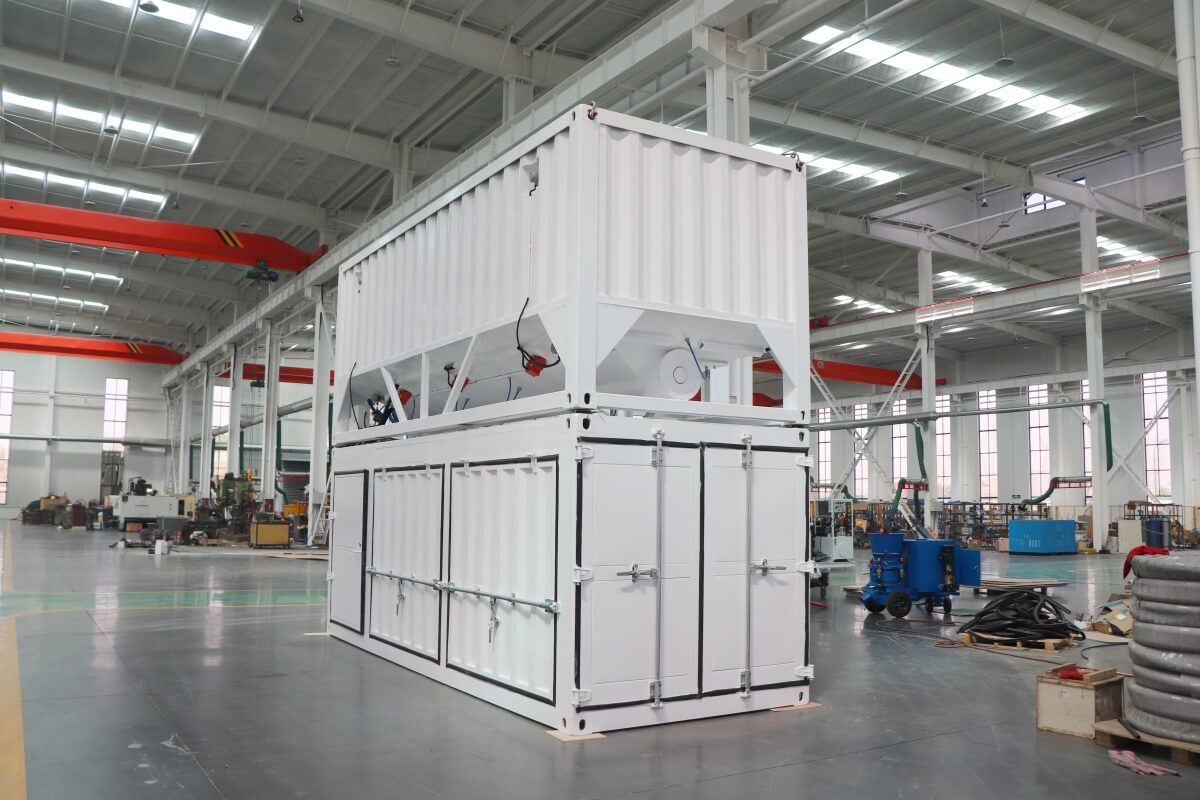
Features of cement grout mixing plant for drilling project:
Real-Time Monitoring and Control:
Sensors monitor parameters such as slurry density, flow rate, and pressure, providing real-time feedback to the PLC. Adjustments are made automatically to maintain consistent quality.
Safety and Environmental Compliance:
The system includes overload protection, emergency stop buttons, and alarms for abnormal conditions. Dust collection and wastewater recycling systems minimize environmental impact.
Core Components
Material Storage and Feeding System:
Cement silos, additive tanks, and water storage units are equipped with screw conveyors or pneumatic systems for automated feeding into the mixer.
Mixing Unit:
A high-efficiency mixer with adjustable blades ensures uniform blending of materials. The mixing time and speed can be customized based on grout requirements.
Slurry Storage and Transfer:
Agitated storage tanks prevent sedimentation, maintaining the slurry’s workability. Progressive cavity or piston pumps transfer the grout to the drilling site, with adjustable pressure and flow rates.
Control System:
The PLC-based control system integrates all components, enabling centralized operation, data logging, and remote monitoring.