Container type grout mixing station is integrated into one or more shipping containers, allowing for easy transportation and quick setup at the project site. Modules can be customized based on project requirements (e.g., single-container for smaller needs or multi-container for larger-scale operations).
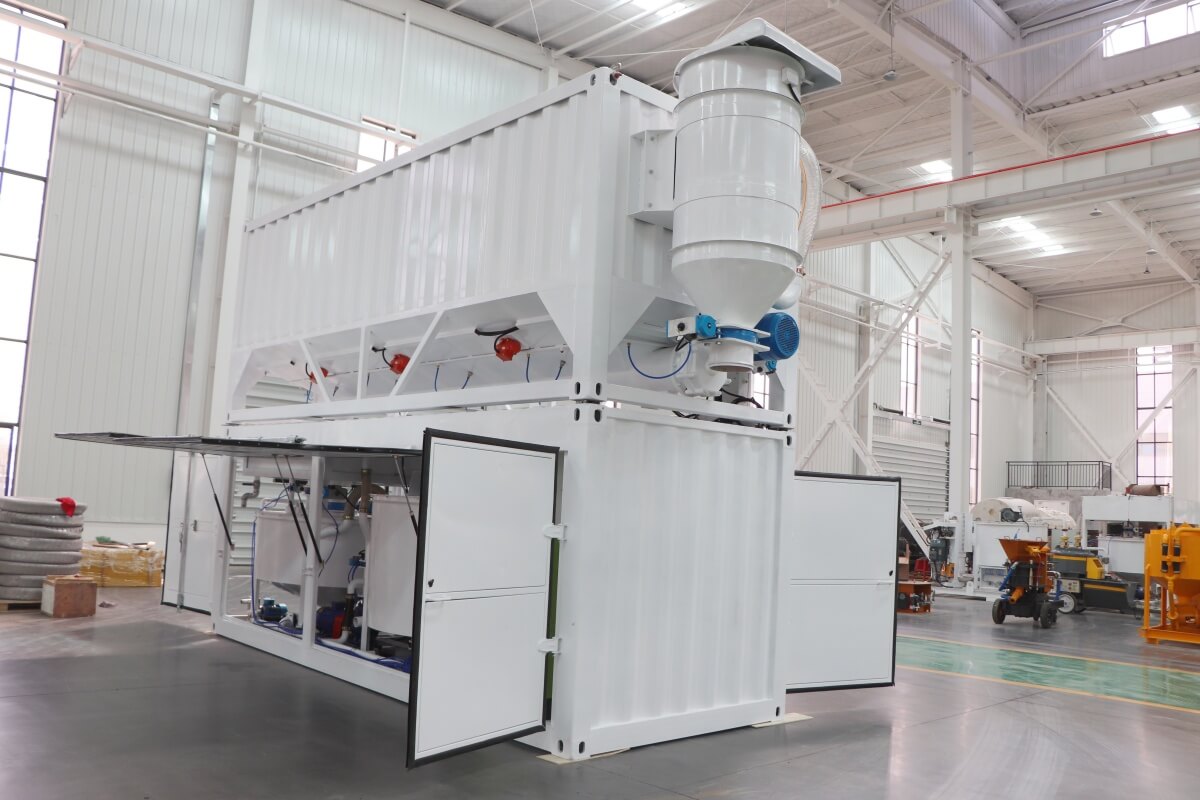
The containerized structure reduces the footprint, making it suitable for confined spaces or remote locations. Easily relocatable via truck, ship, or rail, minimizing downtime during project transitions.
Container type grout mixing station is equipped with advanced mixing technology (e.g., high-speed mixers, precise dosing systems) to ensure consistent grout quality. Automated controls for ingredient proportioning, mixing time, and flow rate, reducing human error and improving productivity.
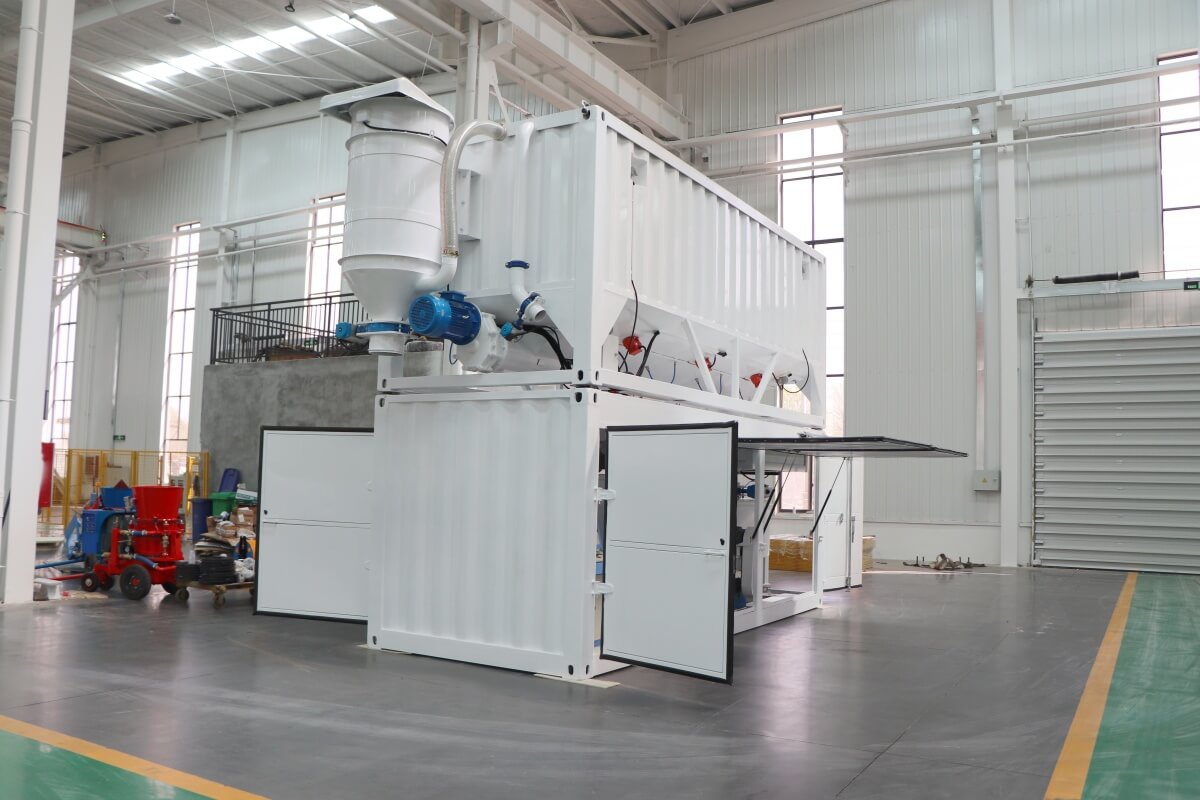
The container enclosure protects internal components from harsh environmental conditions (e.g., rain, dust, extreme temperatures). Robust construction ensures long-term reliability in demanding work environments.
Flexibility to integrate additional modules (e.g., storage tanks, pumps, power generators) based on project-specific needs. Option for dual-component mixing (e.g., cement + water + additives) or multi-material blending.
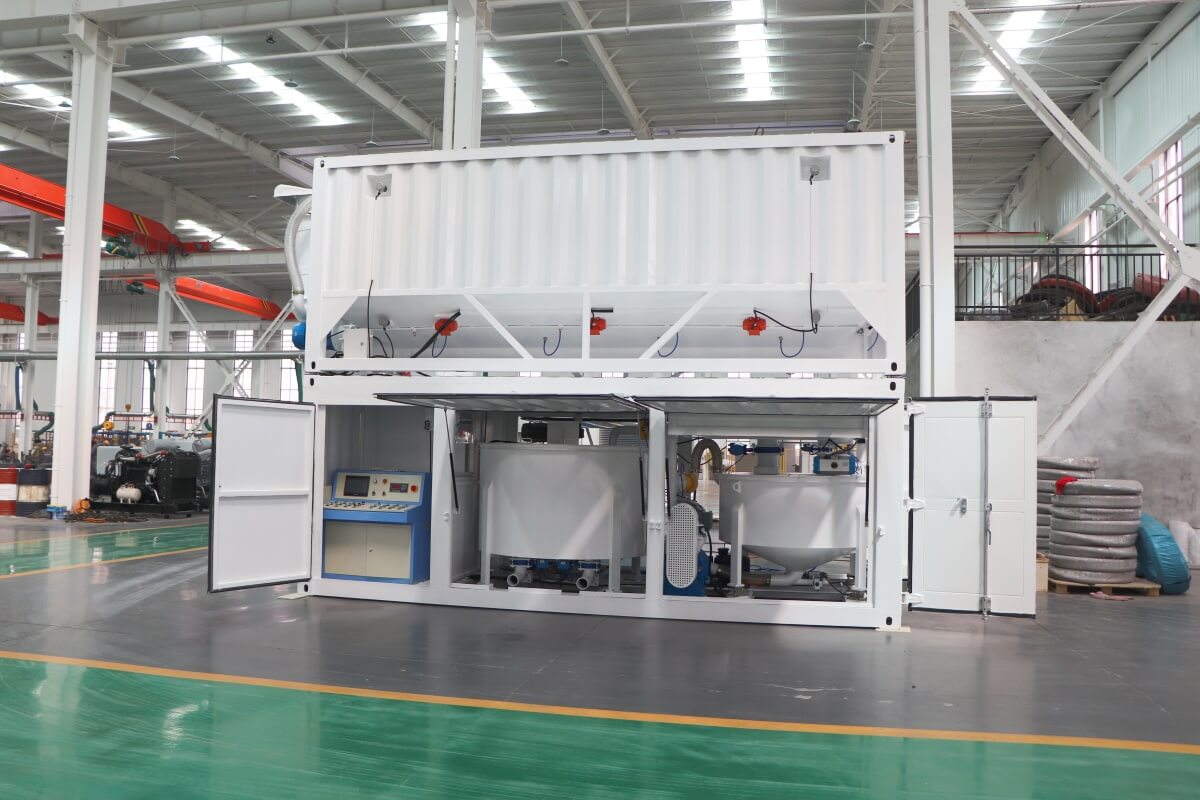
Container type grout mixing station applications:
Underground Construction: Tunneling, mining, and shaft sealing where precise grout injection is critical.
Civil Engineering: Soil stabilization, foundation repair, and anchoring in bridge or building projects.
Oil & Gas Industry: Well cementing, pipeline grouting, and subsea installations.
Geotechnical Projects: Slope stabilization, landfill capping, and void filling.
Renewable Energy: Wind turbine foundation grouting and geothermal well sealing.
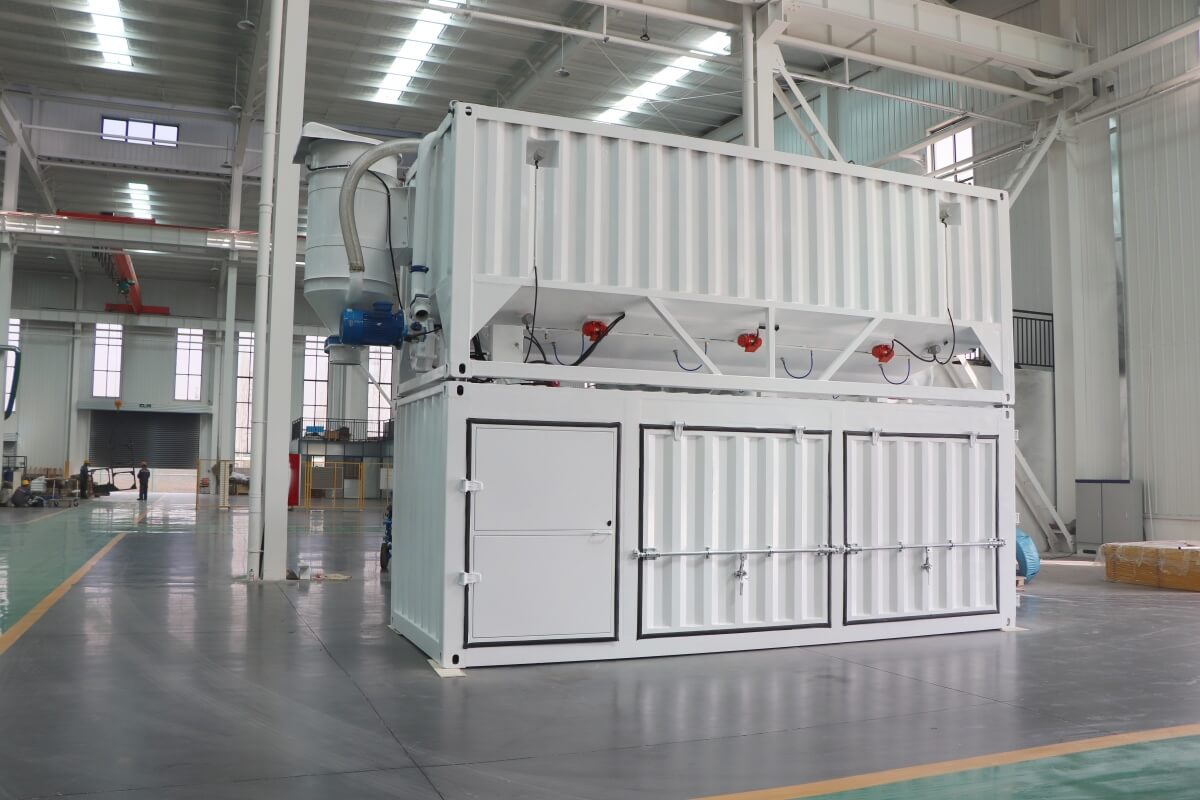